When reflecting on my experiences at Autodesk University last month, it reminded me of how technology dependent we’ve become at telling stories in both the digital and physical worlds. It also illustrated to me that the boundaries between digital and physical modes of communication are becoming less distinct. I heard stories from customers, technology partners and Autodeskers that were weaved into a broader digital tapestry of industry knowledge online. This illustrates to me that the era of connectivity is upon us whether we believe it or not. As discussed in my last blog, there are a number of trends that will change the face structural engineering and they all relate to changes in how we connect with each other and the things around us. The future interplay between technology and people is an important topic of conversation for all of us to have. So why not start that conversation now with AU being fresh in our minds…
We saw nearly 10,000 AEC professionals attending AU this year and over 500 alone attending the MEP & Structural Fabricators Forum. The theme was again focused on the Future of Making Things with a focus on high impact trends like robotics, generative design, machine learning and the cloud (to learn more about AU 2016, please check out this recent post from AECBytes). I saw a common theme emerging at AU where AEC professionals are starting to focus on higher value services, while automating out the lower value services. This is happening out of necessity in order to remain competitive and anticipate the trends discussed above and a few other emergence technologies. I would like to go into a few of these shifts in more depth:
First, I see the adoption of computational design accelerating within engineering firms already using BIM. Computational design is a visual method of programmatically creating, analyzing and choosing model-based designs. Traditionally being viewed as having niche applications for architectural design exploration, we have seen greater adoption by more mainstream engineering teams for “human-centric automation.” What I mean by this is that computational design is enabling teams to automate out routine activities like internal QA/QC processes and data interoperability challenges. This not only improves profitability but also improves the quality of design deliverables.
At the same time, we see computational design adoption helping engineers focus on higher value services. For example, we see engineering firms connecting Dynamo to a range of products like Revit, Robot Structural Analysis and even Advance Steel to explore and refine the best design options for their clients. We also see it helping firms further differentiate their services. . A great example of this was presented by Ben Osbourne, P.E. with Stanley D. Lindsey Associates. I encourage you all to watch this presentation because it is a great example of both computational design’s practical applications in traditional design and novel applications to differentiate extended services.(see Link). Down the road, I expect engineers to offload simpler engineering tasks to computers supported by generative design and machine learning tools. This will empower engineers to tackle more complex problems, especially those dependent upon stakeholders outside of the structure.
Second, I expect to see growing interest and adoption of Level of Development (LOD) based collaboration to automate the verification of BIM data at different stages of the project. The term LOD was created several years ago by the BIM Forum in the US. They created it tohelp create a common language for defining and exchanging model-based deliverables at the BIM object level. As LOD-based model checking technologies like Invicara BIM Assure emerge in the industry, we see engineers and fabricators adopting them to automate QA/QC processes and improve the quality of design deliverables. In the future, we can predict that LOD-based industry standards will help fabricators and contractors accept validated design deliverables. An example of how the structural steel industry is embracing LOD was presented at AU by Will Ikerd, PE, SE with Ikerd Consulting and memberof the BIM Forum (see link).
As LOD-based model checking automates the quality checking of design data, it will also empower engineers to focus on higher value problem solving. Structural engineers will spend more time optimizing their designs not just for code compliance but for constructability factors such as material availability and relative “total installed” cost data. Forest Flager, PhD, with Stanford University’s CIFE program, presented the results of pilot projects that showed significant benefits by optimizing steel frame systems using structural steel availability and cost data (see link). In the end, I see LOD being an important part of the structural design optimization process, both in early design or later when a fabricator is brought on board to deliver greater insight into the fabrication and installation costs. LOD will help establish clear expectations about what level of design information is delivered at different stages of the project.
Third, I see engineers and detailers automating out routine code-based design decisions that also impact detailing and documentation. We saw two examples of this presented at AU by Autodesk technology partners SOFiSTiK and Graitec. Both these companies provide design-driven detailing automation for concrete rebar all within a common BIM environment. As engineers spend less time addressing routine calculation tasks that can be automated, they can focus on more advanced structural analysis methodologies and complex design solutions as presented by ARUP and Autodesk technology partner IDEA RS (see link). Graham Aldwinckle with ARUP discussed the benefits of using advanced computational methods to optimize and analyze complex steel connections. What is novel about IDEA RS Statica Steel is that it allows engineers to more quickly analyze the behavior of complex, non-typical steel connections using researched and validated computational methods. When such technology is connected to BIM, computational design and the cloud, I see engineers in the future able to run more “what if” scenarios of their overall steel frame design that also captures the complexities and impact of the steel connection design. Using a more integrated and iterative process for structural design will free up engineers to spend more time defining what the real problem is and less time crunching through what the possible answers are.
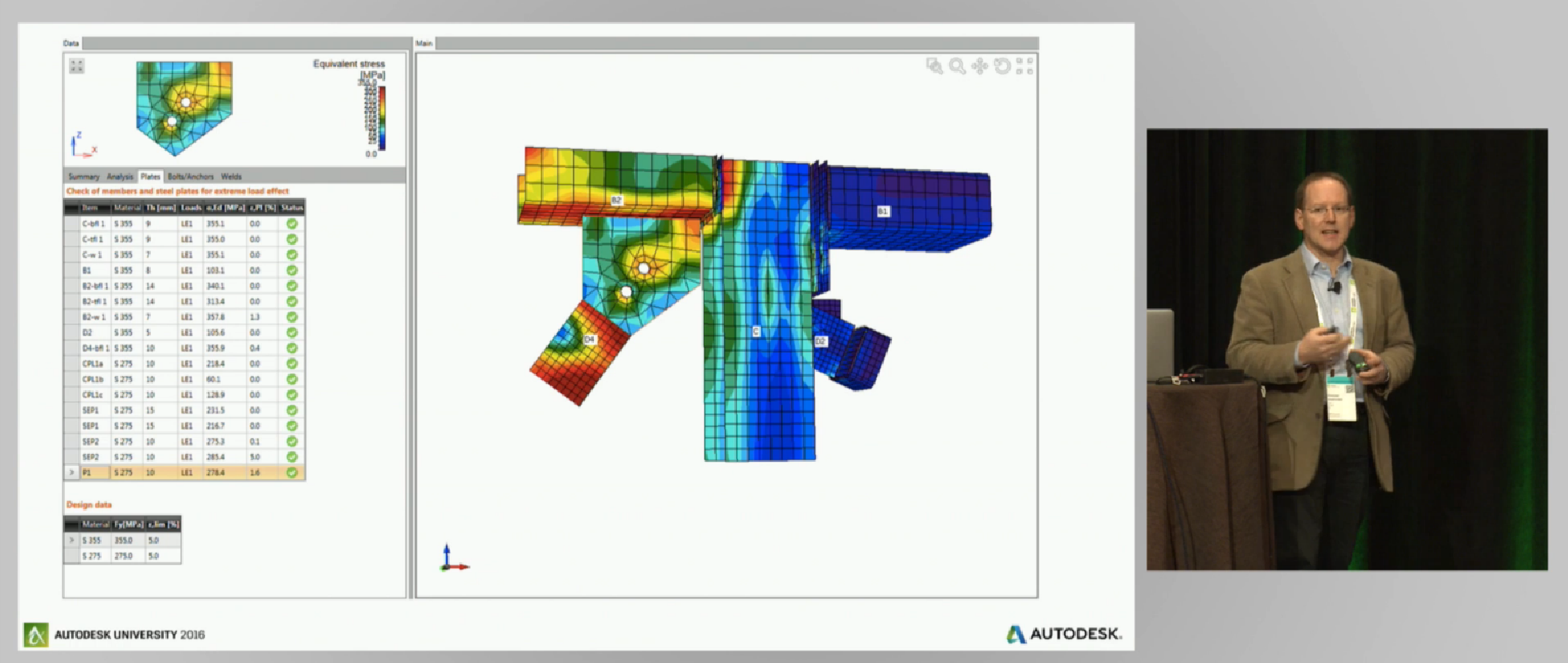
Graham Aldwinckle (Director, ARUP London office) presents an application of IDEARS Statica Steel to analyze existing steel connections as part of forensic engineering services.
Fourth, with the access to greater cloud computing and the adoption of more standardized data models, engineers and detailers will be empowered to automate more of their structural detailing tasks for connection modeling and shop drawing production. As workforces become more global and integrated, we will see more automation in how models are exchanged between regional locations. Doing so will free up detailers to focus on providing higher value services like BIM-centric trade coordination and competence in managing culturally and demographically diverse teams. The development of these skill sets were discussed by steel construction leaders at AU in relation to managing globally dispersed steel detailing teams. Joel Hicks, President of the National Institute of Detailing (NISD) and his peers discussed what NISD is doing to help prepare future steel detailers to work in a growingly more diverse and complex construction industry (see link).
Fifth (and last), the examples above all focus on how software automation is impacting the office. However, we are seeing machine automation on the factory floor as well. Even though the steel fabrication industry has made great strides in becoming more efficient, there is still a great potential to leverage more modern manufacturing technologies like robotics and machine learning. As seen at AU, steel manufacturer FICEP is preparing for this by investing inIFC based fabrication data exchanges. (see link). This will enable greater use of robotics manufacturing on steel factory shop floor such as the assembly of shop parts and welding. As prefabrication of multiple systems including steel grow in the industry, the use of robotics will demand even greater use of BIM
We are seeing this trend of prefabrication happening not just in the factory but also in the field. My favorite presentation at AU this year was a presentation by Marius Jablonskis with Norconsult. Marius presented a compelling story about the design and construction of Vamma 12, a large hydro project in Norway (see link). The Vamma project is unique in that the design deliverables are contractually 100% model-based and do not use paper. By eliminating the need for drawing creation, Norconsult could focus more time on optimizing the design to help the construction teams fabricate and build a better product. This shift away from paper was also seen by the contractors. The formwork supplier fabricated their formwork using Norconsult’s 3D model as a start point, not using drawings. The contractor also used Norconsult’s concrete model to establish survey points that guided the path of the rock excavation machine. This application of subtractive manufacturing principles on the construction site is a great example of how engineers and contractors deliver greater value to their clients in the future.

For their paperless hydro project in Norway called Vammaa 12, Norconsult is using Revit to model all the reinforced concrete in 3D. This model is used by the formwork supplier Doka to more efficiently fabricate the complex formwork. (Images: Courtesy of Norconsult)
I do believe these examples seen at Autodesk University 2016 paint yet another picture of how we will make structural things in the future….and the role of people and technology in doing it. Engineers will need to solve more complex engineering problems and fabricators will have to adapt to more complex collaborative environments, all being driven by trends like prefabrication and globalization of work. They will also need to become better storytellers. The use of more compelling visualization and “storytelling” technology will position engineers and fabricators to be better communicators and leaders on their projects. To differentiate their businesses and ultimately survive, our peers in structural engineering and fabrication must shift their efforts to high-value services and automate the low-value services.
So do you agree? Are you seeing this trend happening around you? I would love to hear your feedback about this topic.
The post AU 2016 Gives a Glimpse into the Future for Structures appeared first on BIM and Beam.
from my Autodesk source Bim & Beam: BIM and Beam at http://blogs.autodesk.com/bim-and-beam/2016/12/22/au-20176-gives-glimpse-future-structures/
via IFTTT
No comments:
Post a Comment