The new release of Advance Steel 2018 has been out for a few months now. Here is a highlight of the top 10 features in case you haven’t had the chance to get familiar with them yet.
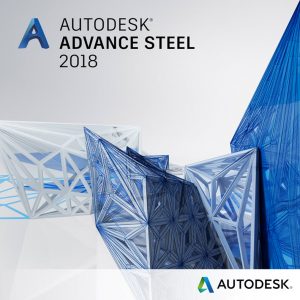
1 – One Advance Steel installation
By combining the functionality of the two products into a single executable, there is no need any more for customers to separately install both AutoCAD 2018 and Advance Steel 2018 software on their desktop.
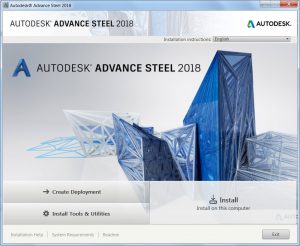
When you install Advance Steel 2018 you will see an icon for Advance Steel on the desktop. Selecting the Advance Steel icon will give the user access to the Advance Steel and embedded AutoCAD functionality.
Tip: users who would like to run just the AutoCAD functionality of the product can select ‘Autodesk Advance Steel 2018 – AutoCAD’ from the Start Menu.
2 – Migrate custom settings tool
The Migrate Custom Settings tool offers a modern and informative interface for migrating your custom settings and files from a previous release to Advance Steel 2018.
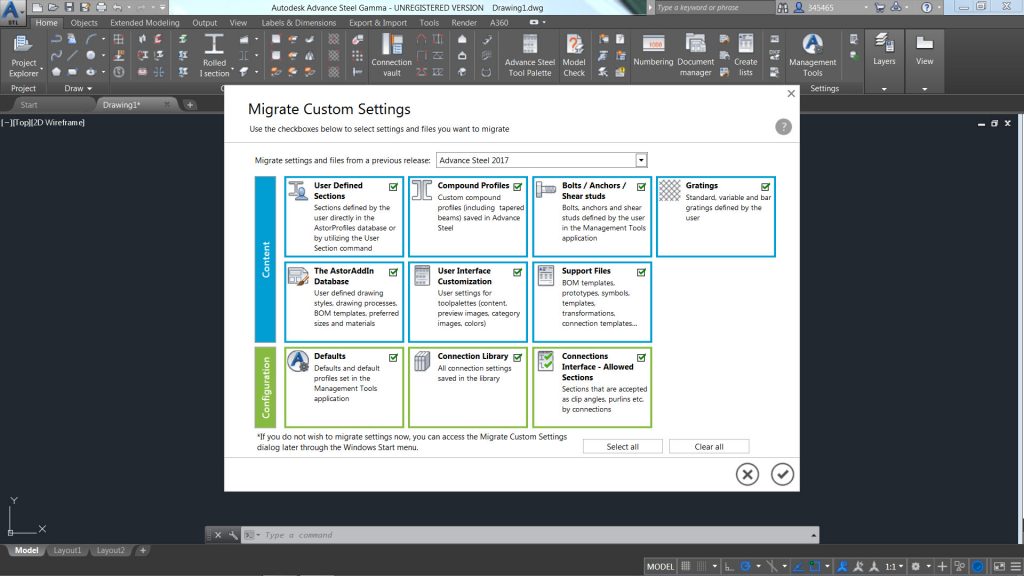
It helps detect and identify customized settings and enables you to choose which ones you would like to migrate. A summary report created from the migration offers comprehensive information in an easy-to-read format.
Tip: If you change your mind about migrating settings from a previous release, you can easily restore Advance Steel default settings using the Reset tool, which is available from the Start menu.
3 – Combine model views with cameras
Model views combined with cameras help simplify the process of creating general arrangement drawings.
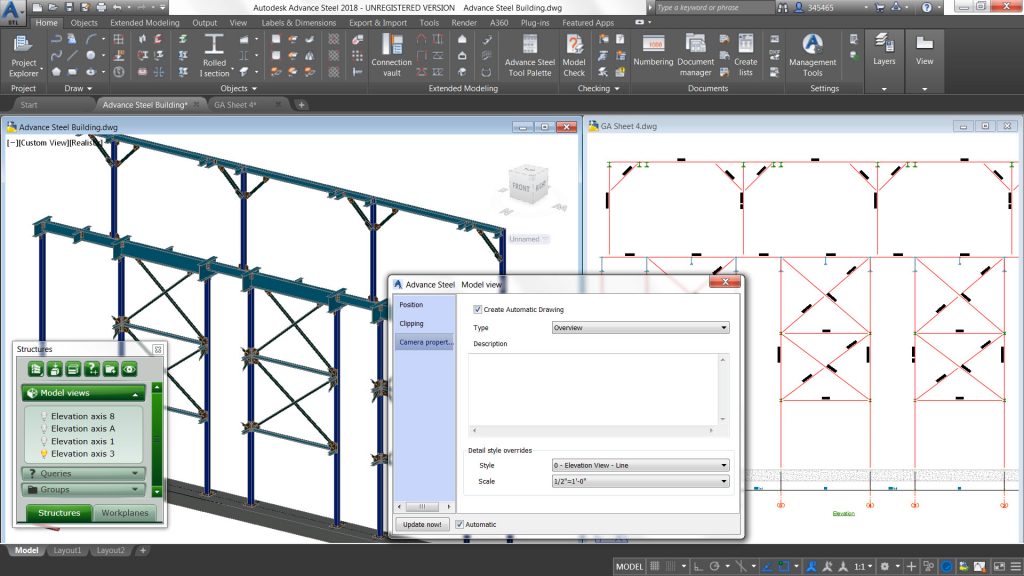
Advance Steel 2018 now enables you to combine a model view with a camera and use it for drawing creation by assigning it a specific drawing style & scale. By using a Drawing Process, you can automate the creation of general arrangement drawings based on these cameras. As a result, you get drawings automatically labelled and dimensioned based on your preferences.
4 – Call out on drawing
With the new “Create callout view” feature, you can now create a call out view from a 2D view or 3D view directly within the drawing.
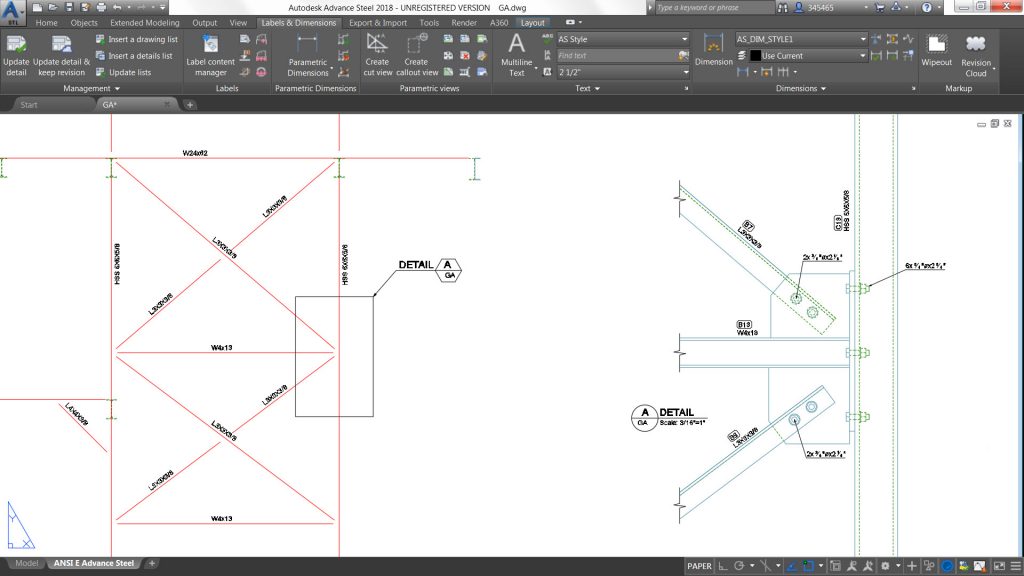
Once you have created the call out, you can move the title placement with its grip and you can control the frame appearance and change it – for example from a rectangle to a circle or vice-versa.
This new feature helps you create more compelling drawings more quickly and easily.
Tip: when creating the call out, by pressing S like Settings, you can access a dialog where you can specify the scale and assign a specific presentation to be used.
5 – Drawing styles for manual cut views on drawings
Advance Steel 2018 offers the possibility to better control ready-to-use presentations available when adding a manual cut or a call out view on a drawing.
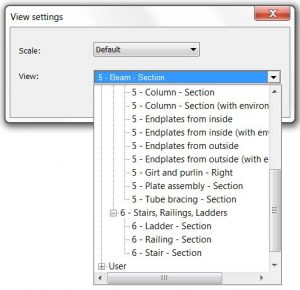
The drawing styles manager enables you to select which view presentations you would like to have available with a new option “Used for Cuts and Callouts” located under “View properties” tab.
When inserting a manual cut or a call out view within a drawing, press S like Settings to access the “View settings” dialog containing the predefined view templates and select the one you want to use for the view you add to the drawing.
6 – Enhanced local content for the US market
The weld symbol has been enhanced (text & symbol size) to match better local requirements.
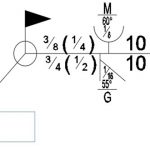
The US release is also delivered with dedicated drawing styles for shop drawings of U and C shape beams. It also has some presentation enhancement such as the hatch pattern representation for holes on shop drawings.
7 – Multi-ball stanchions handrail
Advance Steel 2018 provides a new automatic & parametric macro for inserting prefabricated ball stanchions.
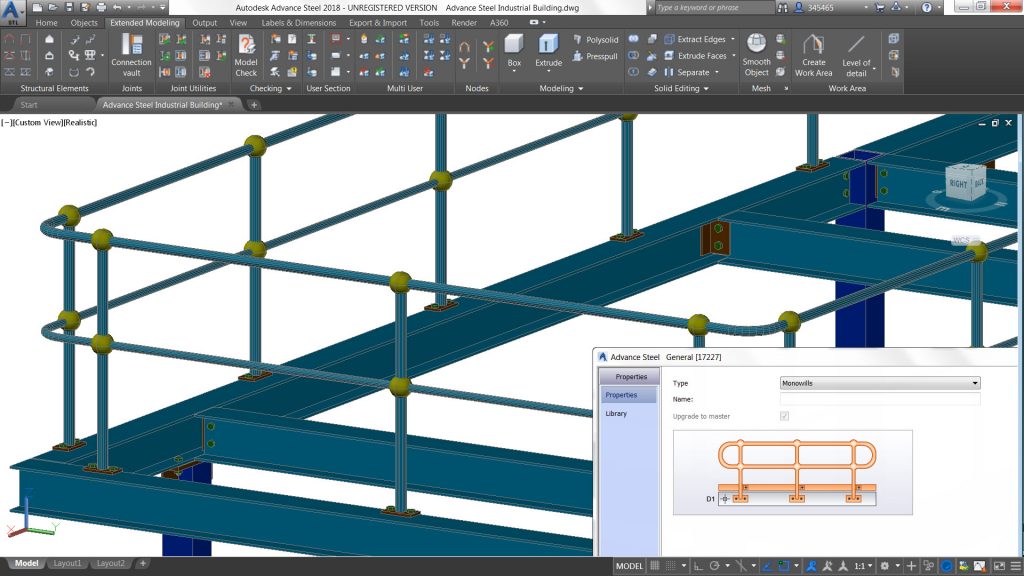
These ball stanchions are from Australian & New Zealand providers and are inserted as special parts in the 3D model.
8 – Cold rolled purlin connections
Advance Steel 2018 provides a new automatic & parametric connection for cold rolled sections (such as purlins and side rails).
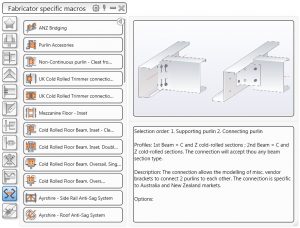
The connection can be started from the Connection vault and offers various options in regards to the brackets (from Australia & New Zealand) available by default.
Tip: It is easy to adjust the settings from the properties dialog box, you can add more vendors within the database controlling the macro.
9 – Custom objects stored in the DWG file of the 3D model
If your Advance Steel model contains custom properties such as custom sections or materials, you can choose to write this information in the DWG file so that other project team members or stakeholders can visualize the entire model in other products such as Navisworks, AutoCAD Plant 3D, BIM 360, or A360 Viewer.
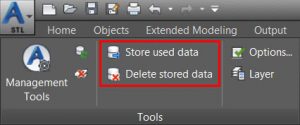
Tip: if you change your mind about including custom properties in your Advance Steel DWG file, you can use the “Delete stored data” icon available in the User Interface.
10 – Localized online help documentation
The online help documentation, which has been available only in English until now, is also available in French and German languages.
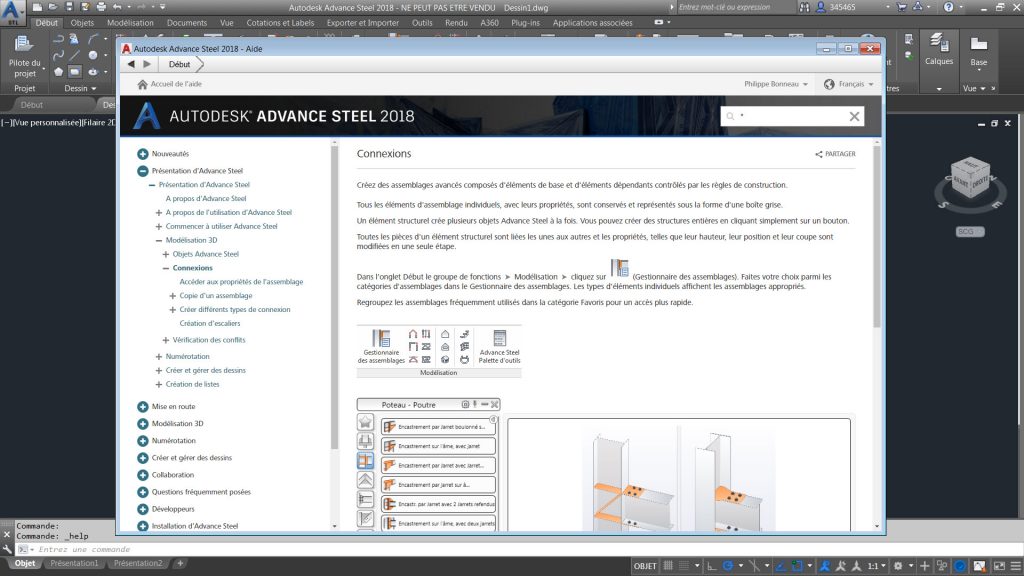
If you want to see some of these features in action, watch the Advance Steel 2018 New Features playlist on YouTube.
The post Top 10 Features in Advance Steel 2018 appeared first on BIM and Beam.
from my Autodesk source Bim & Beam: BIM and Beam at http://blogs.autodesk.com/bim-and-beam/2017/10/18/top-10-features-advance-steel-2018/
via
IFTTT